


smaRTE
STOCK

Accurate, high-speed stock counting, tracking, and tracing to improve stock replenishment, while reducing unnecessary manual counting, shrinkage, and high safety stock levels costs.
READ MORE

smaRTE SPLICE
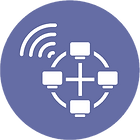
BACKGROUND
Up until recently, most cyberattacks have been focused on accessing data within the IT environment through various means and for various reasons. Operational Technology (OT) has also tended to remain separate from IT, even employing independent communication infrastructure that usually focuses on local interaction between machines and the engineers that are operating them.
However, there has been a drastic shift recently towards merging IT with OT, as the OT equipment becomes more intelligent and connected. This brings with it a major security risk to the business that traditional IT CyberSecurity solutions are not designed for. Even though IT systems are "air-gapped" and "ring-fenced" with firewalls etc, OT systems are now bridging this gap to IT and this creates vulnerabilities to both the IT environment and, even more concerningly, to the OT environment. If hackers can gain unauthorised access to certain OT equipment, this will not only result in loss of data and privacy, but major risks to production, company credibility, loss of income, and even human lives.
WHY YOU SHOULD CONSIDER OT CYBERSECURITY
Cyber attacks on OT environments are becoming increasingly common. According to Gartner, these cyber-attacks have evolved from immediate process disruptions such as shutting down a plant to compromising the integrity of industrial environments with the intent to create physical harm.
It is therefore critical that an OT-focused cybersecurity solution is employed that not only
detects but also prevents all connected OT equipment from becoming vulnerable to cyber-attacks. This in turn will ensure the cyber-physical resilience of both your IT environment AND your entire OT environment. This will also minimise the risk of equipment downtime and therefore, assist to maximise the return on all your operational assets.
The following are common operational vulnerabilities inherent in OT environments:
-
Unpatched (vulnerable) code running on Data Historians, Engineering and Operator Stations, Human-Machine Interface (HMI) panels, and Programmable Logic Controllers (PLC) that most likely do not have patches available.
-
Unsecured configurations aimed to ensure interoperability between different vendor equipment.
-
Fragmented and unprotected identities - sometimes unchangeable vendor defaults.
-
Unauthenticated and unencrypted Industrial Control Protocols.
An adversary with a foothold on the network can leverage any of these inherent
weaknesses to:
-
Take over normal operations.
-
Disrupt normal operations (this can be achieved without a deep understanding of the industrial process, with reusable attack tools, such as Pipedream).
-
Hold the production line to ransom - Operating logic can be changed and Engineers can be locked out of the PLCs.
-
Steal intellectual property, such as by exfiltrating confidential design and process documentation.
-
Cause damage, destruction, or unsafe working conditions by manipulating the state of the managed process and blinding operators to the real state of the process.
OUR SOLUTION
FLEX Digital offers a proudly South African, revolutionary OT Cybersecurity solution that is one of only four in the world that employs Artificial Intelligence to not only detect OT cyber attacks but prevent them in real-time.
Our smaRTE Splice solution actively prevents cyber-physical attacks through proactive vulnerability shielding inside an encrypted overlay network. This allows you to embrace connection and convergence, rather than shy away from it. It is the logical alternative to air gaps, firewalls, data diodes, and old-school thinking. The solution comprises three layers with three operating modes as can be seen below:
